Why Magnetic Separation Technology is Crucial in the Mining Industry
One of the significant challenges faced by mining operations is how to accurately distinguish between useless materials and valuable resources from the mixed products generated during extraction. Whether through open-pit or underground mining, mining activities produce large amounts of waste, including both low-value minerals and non-recyclable man-made waste. These wastes are often tightly interwoven with valuable minerals, making them difficult to separate. Magnetic separation technology is perhaps the most effective means of addressing this issue.
Magnetic separation plays a key role in efficiently separating iron and other magnetic materials from ore, ensuring that only valuable minerals are processed further. It works by using magnetic forces to attract magnetic particles, which can then be separated from non-magnetic materials. This method significantly improves the efficiency of the mining process by:
1. Reducing Waste: By removing unwanted materials early in the process, magnetic separation helps reduce the volume of waste that needs to be dealt with. This not only saves time and energy but also lowers the environmental impact of mining activities.
2. Improving Resource Recovery: Magnetic separation enables the extraction of valuable minerals that may otherwise be lost or mixed with non-valuable materials. This can significantly increase the yield of usable resources, making mining operations more cost-effective.
3. Enhancing Efficiency and Safety* By streamlining the separation of materials, magnetic separation technologies help improve the overall efficiency of the mining process. Additionally, by removing metallic debris and contaminants early, it helps prevent damage to equipment and reduces safety risks associated with handling hazardous materials.
4. Cost-Effectiveness: Compared to traditional methods, magnetic separation is cost-effective as it often requires less energy and fewer resources. It can be applied at various stages of the mining process, providing a flexible solution for both large-scale operations and smaller, more specific mineral extractions.
In summary, magnetic separation technology plays a pivotal role in the mining industry by improving resource recovery, reducing waste, and increasing efficiency, making it an indispensable tool in modern mining operations.
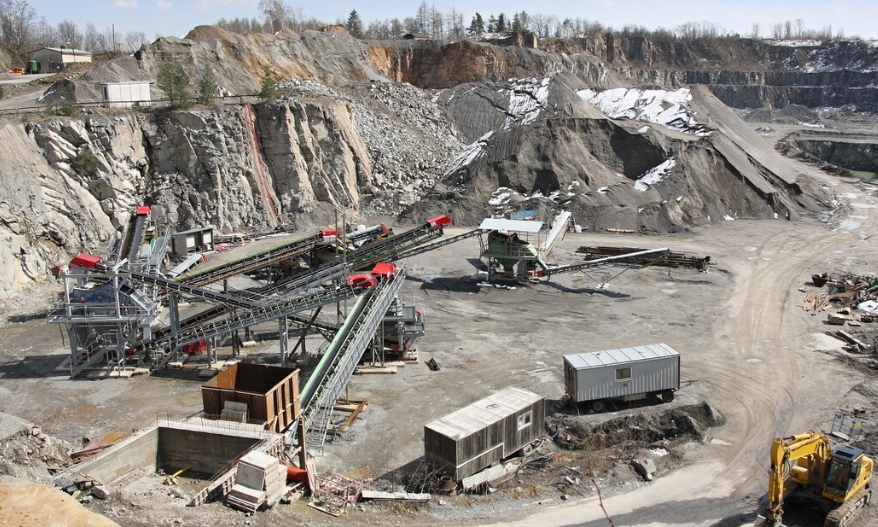
Magnetic Separation Technology Unveiled
Magnetic separation is a method that uses magnetic forces to remove metal or ferrous components from a mixture. This technology plays a vital role in various industries, especially in mining and material processing, by ensuring that only valuable minerals are processed, while contaminants and metals are effectively separated.
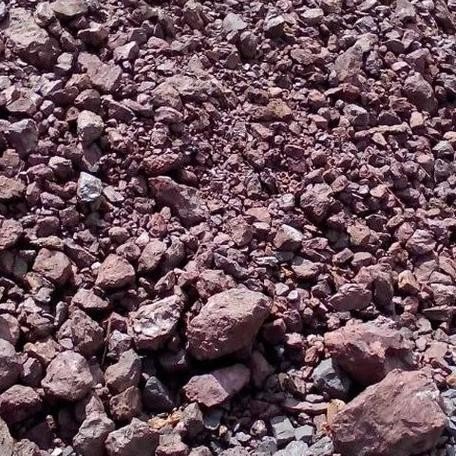
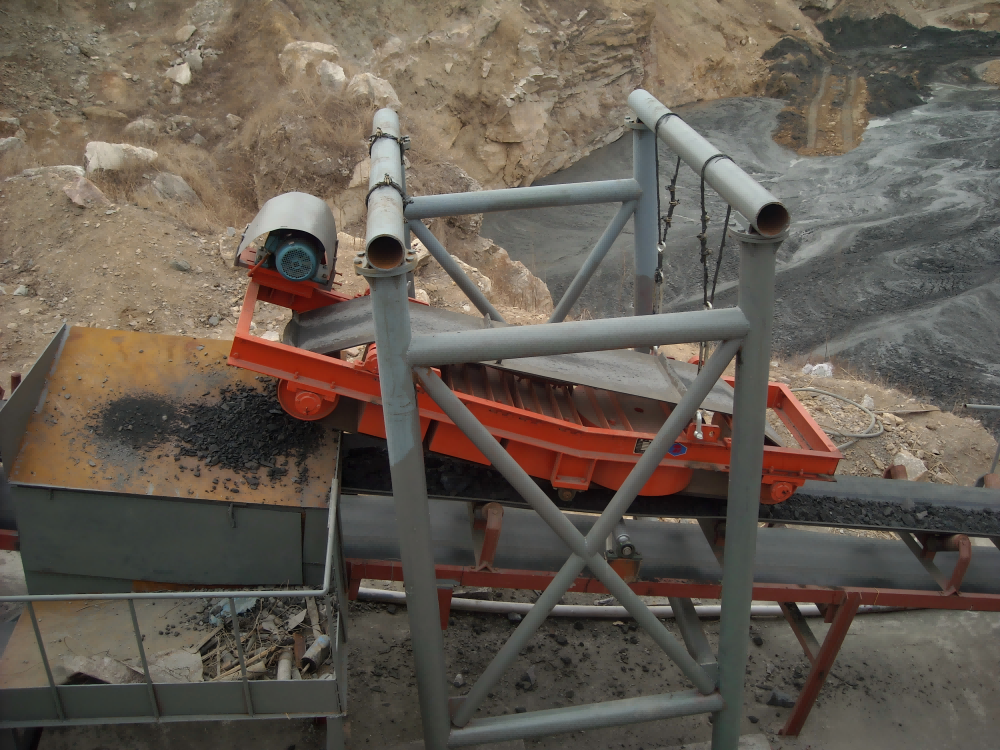
How Magnetic Separation Works
Magnetic separation equipment typically consists of several components, including a vibrating feeder, two conveyor belts (upper and lower), and a magnetic field device. The raw materials are fed onto the lower conveyor belt via the vibrating feeder. As the material moves along the belt, the magnetic field attracts any magnetic particles (such as metals) to the upper conveyor belt, thus effectively separating the unwanted metal from the rest of the raw material.
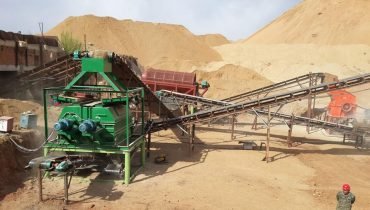
Operation Mechanism of Magnetic Separation Technology in Mining
In the mining industry, magnetic separation is mainly used to remove "impurity minerals" or unwanted metal waste from the raw materials extracted during mining. These impurities are often the result of artificial waste generated during mining operations, such as wires from explosives, nuts and bolts, nails, or the sharp tips of heavy extraction tools. Magnetic separation devices are typically placed at the beginning of the raw material processing line in mining operations to ensure that these unwanted materials are removed before they can damage downstream equipment such as crushers and conveyor belts. This is crucial because such equipment is highly susceptible to damage from metal fragments or sharp objects.
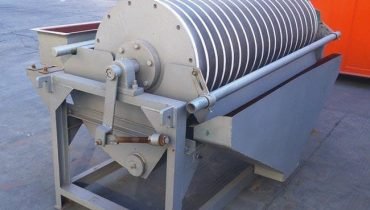
Integration with Existing Systems
One of the major advantages of most magnetic separation systems is that they are designed for easy integration into existing production and conveying systems. This means that significant changes to equipment or production lines are unnecessary, making the technology both cost-effective and easy to implement. In summary, magnetic separation is a crucial technology that ensures the protection and efficiency of mining and material handling systems. By effectively removing ferrous material contaminants, it improves the overall quality of the processed materials and reduces the risk of equipment damage.
Types of Magnetic Separation Equipment
The type of magnetic separation equipment used in mining operations depends on the types of minerals being extracted and the quantity of impurity minerals generated during the process. Consequently, the magnetic flux or power of the equipment can vary. Generally, magnetic separation equipment can be categorized into two main types: electromagnetic and permanent magnet.
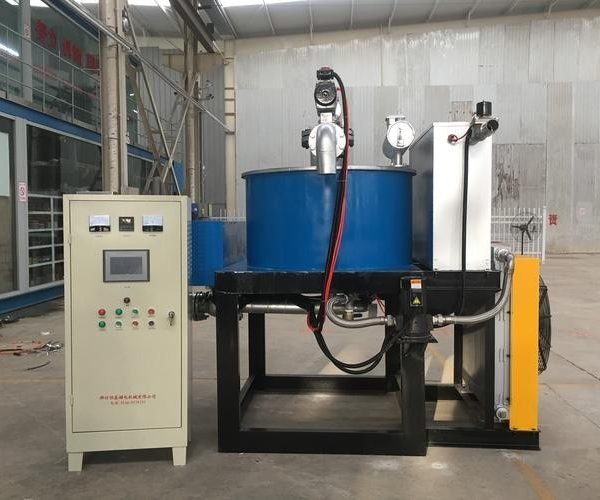
1. Electromagnetic Magnetic Separators
Electromagnetic separators use alternating current (AC) and direct current (DC) to generate a magnetic field. These devices are particularly effective for removing large chunks of ferrous material or impurity minerals from raw materials. They are often suspended above conveyor belts, where they attract unwanted materials upwards, thus separating them from the rest of the material flow. One of the key benefits of electromagnetic separators is the ease of cleaning. Once the power supply to the electromagnetic field is turned off, the magnetized materials can be removed without much effort. This makes the equipment easy to maintain and operate, especially in high-volume production environments.
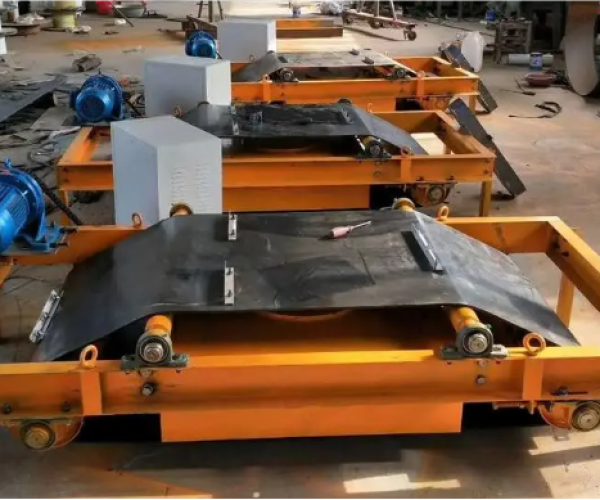
2. Permanent Magnet Magnetic Separators
Permanent magnets are made from materials that naturally generate their own magnetic field. Although the magnetic force of permanent magnets is not as strong as that of electromagnetic separators, they are particularly effective at attracting ferromagnetic materials such as nickel, cobalt, iron, and certain rare-earth metals. Some modern permanent magnets are made from rare-earth materials, which have significantly stronger magnetic fields compared to traditional materials. These powerful magnets can even attract stainless steel, which is typically non-magnetic. However, to maintain the efficiency of permanent magnets, it is important to regularly clean the magnetic surface to remove accumulated metal residues.
Both electromagnetic and permanent magnet magnetic separators have unique advantages. Electromagnetic separators are preferred for handling larger, more substantial impurity materials and offer ease of maintenance, while permanent magnet separators excel at extracting fine ferrous and rare-earth metals, especially in situations where strong, consistent magnetic fields are required. The choice between the two types of separators is determined by the specific requirements of the mining operation, including the size and nature of the impurities and the type of minerals being processed.
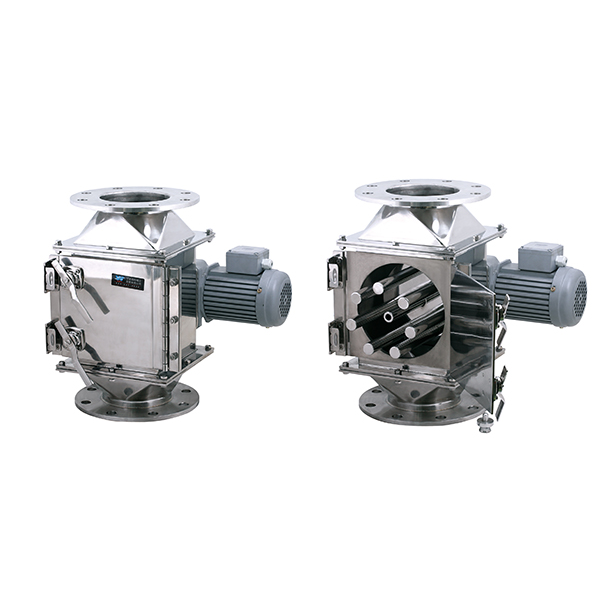
Magnetic separation technology, due to its cost-effective and efficient separation capabilities, has been widely applied in many industries. In particular, in the aggregate and mining sectors, the need to remove ferrous metals mainly arises from the protection of processing equipment such as conveyors, screens, and crushers. Metals mixed in the material, such as bucket teeth, may cause significant damage, leading to expensive downtime and repair costs. Another advantage of magnetic separation technology is its ability to improve product purity.
Protecting Processing Equipment
In the aggregate and mining industries, the removal of ferrous materials is primarily aimed at protecting processing equipment like conveyors, screens, and crushers. As raw materials are processed, magnetized materials (such as bucket teeth, nails, or steel wires) can cause serious damage to equipment. These metal fragments not only wear down components but also cause equipment downtime, resulting in high maintenance costs and production interruptions.
By using magnetic separation technology, these magnetic contaminants can be effectively removed from the raw materials, preventing them from damaging processing equipment, thus extending the equipment’s lifespan and reducing maintenance costs.
Improving Product Purity
Magnetic separation technology also improves the purity of the final product. In processes like mining and aggregate production, the presence of iron impurities can affect the quality of the end product. Magnetic separation equipment can effectively remove these impurities, ensuring the product meets quality standards.
For industries that require high-purity raw materials, such as construction materials, chemicals, and manufacturing, the use of magnetic separation technology significantly improves product quality and enhances market competitiveness.
Magnetic separation technology not only protects processing equipment, lowering repair and downtime costs, but also improves the purity of the final product, meeting the industry’s demand for high-quality output. This makes magnetic separation technology an indispensable solution in the aggregate and mining sectors.