Metal Impurities in Glass and Sandstone and Their Effective Separation
Glass products are mainly divided into two categories: flat glass and container glass. In the production process of flat glass, metal impurities may originate from aluminum components (such as aluminum parts in insulated glass), sensors, connectors, car window frames, as well as lead elements in wired glass or colored glass. In the production of container glass, metal impurities may be introduced by steel crown caps, aluminum screw caps, or steel and stainless steel brackets.
As the market demands increasingly higher quality for recycled glass as secondary raw materials, the recycled glass must be nearly free of ferrous or non-ferrous metal impurities. To obtain high-quality pure glass, the removal of metal impurities is crucial. Similarly, removing iron from mineral materials like sand and gravel is essential, as iron tends to rust in construction materials, affecting their appearance and longevity. Magnetic separation is an effective method for this process, ensuring that iron particles are removed from raw materials like glass, sand, and gravel.
Ceramic blasting media and casting sand can also become contaminated during production, resulting in large amounts of material being discarded and sent to landfills, which not only wastes resources but also takes up valuable landfill space. Magnetic separation equipment provides an efficient way to eliminate such contamination, improving material quality and sustainability.
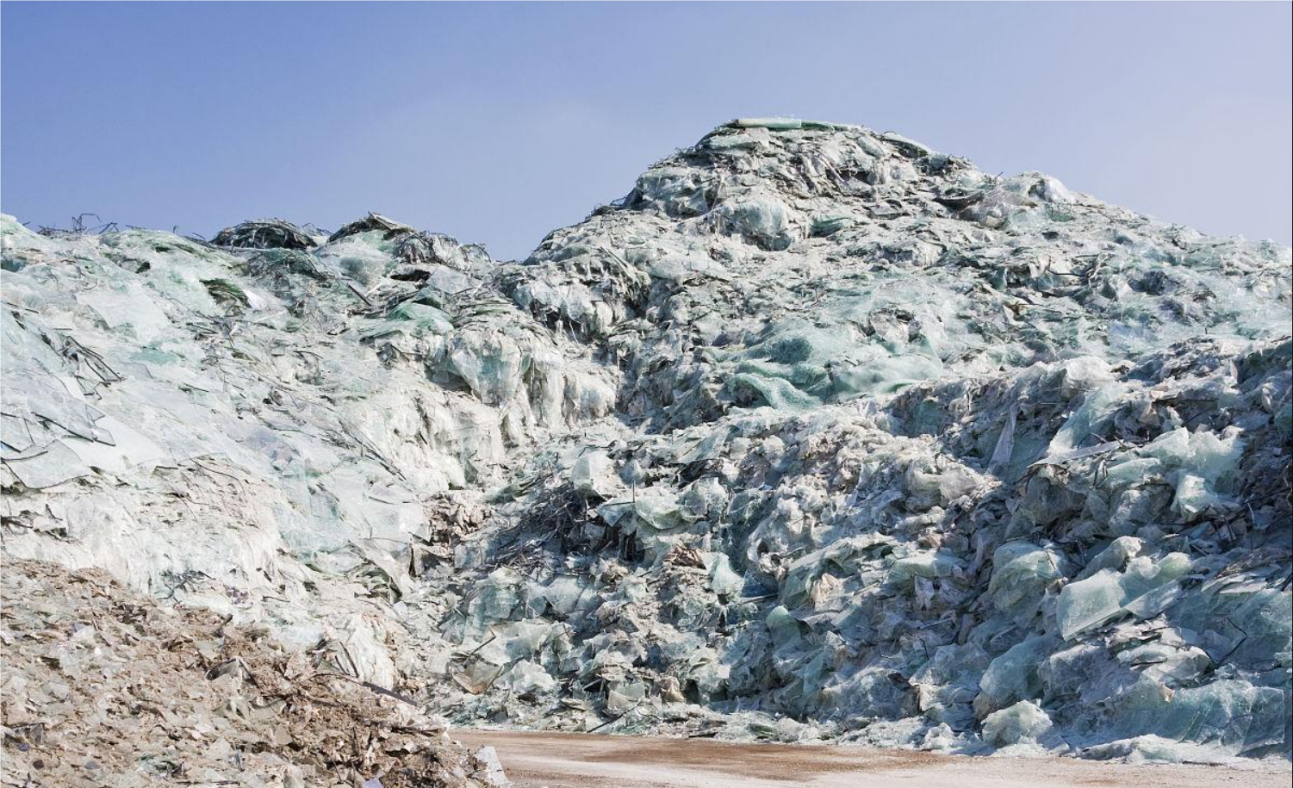
Key Technologies for Metal Impurity Separation
To effectively separate these metal impurities, we use durable magnetic separators equipped with wear-resistant replacement parts, such as high-intensity magnetic separators and magnetic head pulleys. In the process of metal separation from glass, mineral, and ceramic materials, the magnetic separator's resistance to material abrasion is critical. This is key to ensuring long-term stable operation and reducing maintenance costs.
The wear-resistant sheath of our magnetic separators is made of manganese steel. This design allows the wear-resistant casing to be easily replaced without the need to change the entire magnetic drum, significantly saving time and costs. Additionally, we can manufacture other parts of the magnetic separator, such as magnetic bar sleeves, chutes, and separation plates, from manganese steel according to customer requirements.
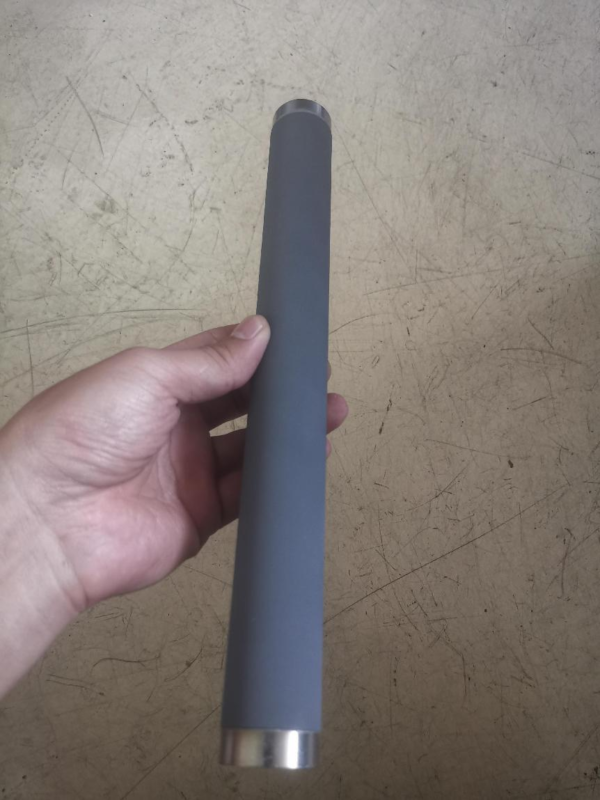
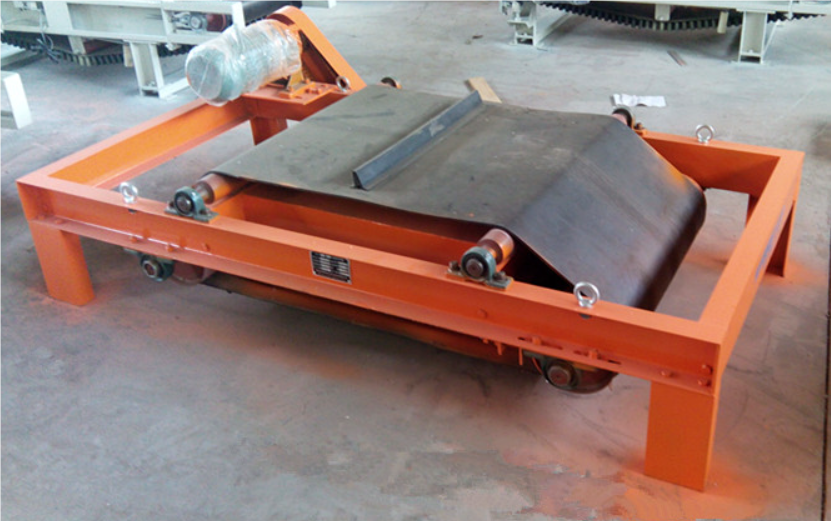
Belt Magnets for Coarse Ferrous Metals
For coarse and exposed ferrous metals (greater than 1 mm), we use reliable belt magnets for separation. These permanent magnets create a strong magnetic field that is ideal for separating larger iron particles. Belt magnets are widely applied in the glass industry, sand, and gravel production lines due to their reliability and cost-effectiveness. Belt magnets can be easily and quickly installed above conveyor belts with minimal adjustment to the production line, ensuring efficient removal of metal impurities while minimizing product loss.
Drum Magnets and Magnetic Head Pulleys for Fine Particles
For fine or hard-to-separate iron particles, we use drum magnets or magnetic head pulleys for precise separation. These devices can handle complex materials, such as glass containing metal wires, achieving efficient iron removal. Drum magnets are particularly effective for fine magnetic particles, as they provide strong magnetic fields that can separate even small ferrous contaminants from raw materials. Magnetic head pulleys can be used interchangeably with the existing conveyor return rollers or purchased as complete systems. To ensure optimal separation efficiency, attention must be given to matching layer thickness, belt speed, and capacity during installation. The separation of iron parts can be optimized by adjusting the belt or drum speed and the positioning of the separating baffles.
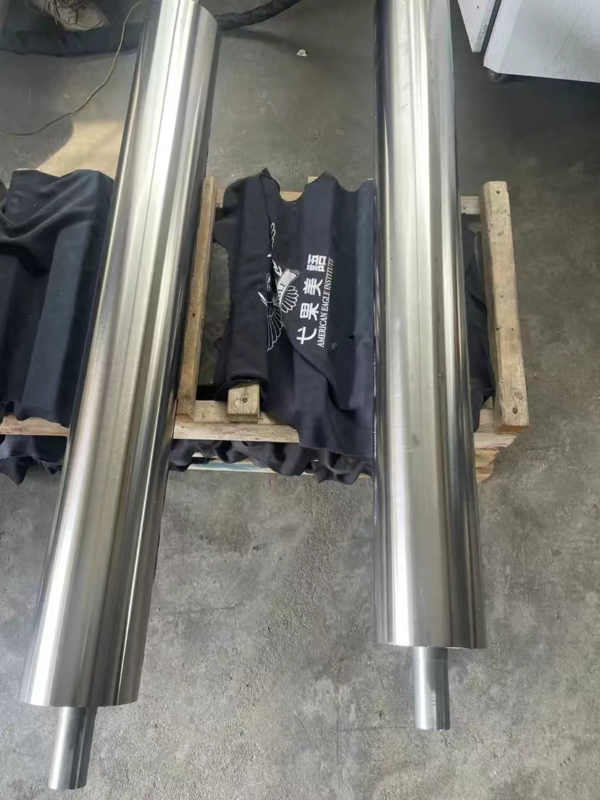
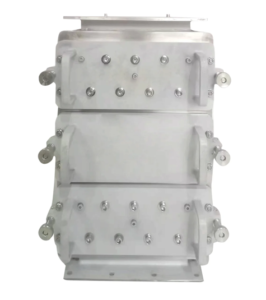
Drawer-Type Iron Separators with High-Gradient Magnetic Bars
For extremely small iron particles and weakly magnetic materials, such as stainless steel, we have developed drawer-type iron separators equipped with high-gradient magnetic bars. This magnetic system is extremely powerful, capable of removing tiny encapsulated iron particles from glass, sand, and gravel. The system not only offers wear resistance but also precisely handles fine iron and weakly magnetic particles. This technology is ideal for upgrading ceramic blasting media or casting sand, effectively separating large amounts of stainless steel and fine iron particles, improving material recyclability. The high-gradient technology often delivers impressive results, and we offer testing services to ensure the certainty of the final outcome for our customers. By efficiently removing iron and other contaminants, we help our clients achieve high-quality raw materials for both the ceramics industry and glass industry, improving their product quality and overall efficiency. Through the implementation of these magnetic filters, the separation efficiency of ferrous and non-ferrous contaminants is greatly enhanced, ensuring that the end product meets the highest standards. Whether for glass production, ceramics production, or plastics recycling, our magnetic separators are designed to meet the rigorous demands of various industries, offering a reliable solution for impurity removal.