Chemical Industry
In the chemical sector, metal impurities, such as ferrous contaminations, are a common source of many challenges. By employing magnetic technology, even the tiniest metal particles can be effectively removed without compromising the core properties of the raw materials.
Impact of Metal Contamination
Metal corrosion can alter the color of cleaners or coatings. In turbine and engine combustion processes, metal particles can cause significant damage to the processing of natural gas and petroleum. Additionally, unwanted metal particles can disrupt the properties of various products. For example, in battery manufacturing, metal impurities can affect the conductivity of carbon black. Similarly, in plastic production, metal particles can reduce the insulation performance of cables.
The application of magnetic technology provides a reliable solution to prevent these issues, including the use of grate magnets and magnetic separation systems designed to remove even the smallest metal contaminants efficiently.
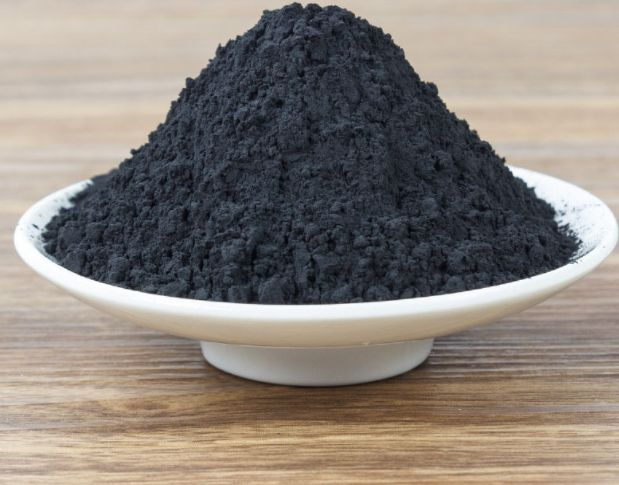
Advanced Material Purification and Filtration Solutions
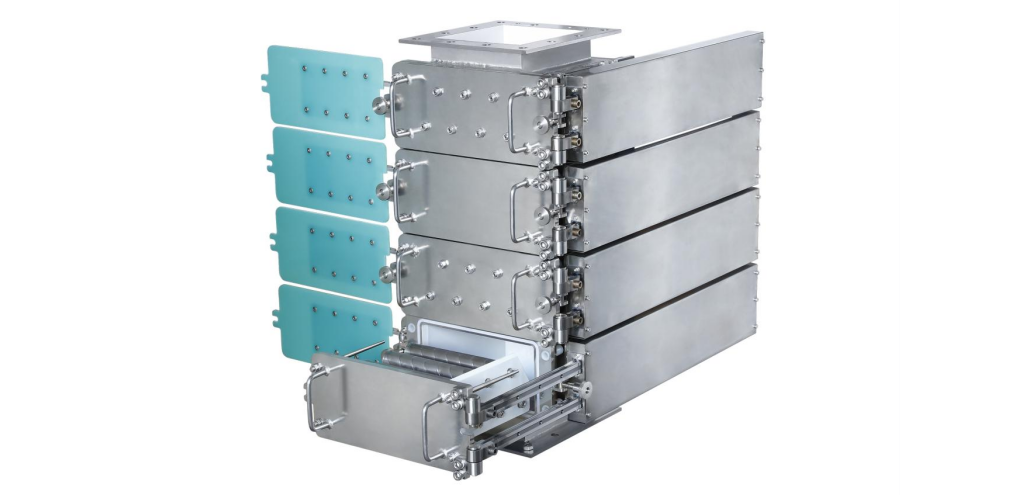
Magnetic Filtration Systems
Magnetic filtration systems offer highly precise and efficient solutions for removing rust and weakly magnetic metal particles from chemicals. They are also valuable for recovering ferromagnetic catalysts, thus protecting equipment from damage and reducing operational costs. Careful selection of the magnetic materials is essential, especially since some products may be corrosive and could harm seals or housings. These systems should also feature self-cleaning capabilities, such as self-cleaning magnetic separators and be able to operate under high-pressure conditions. We offer a variety of magnetic separation systems tailored to different needs.
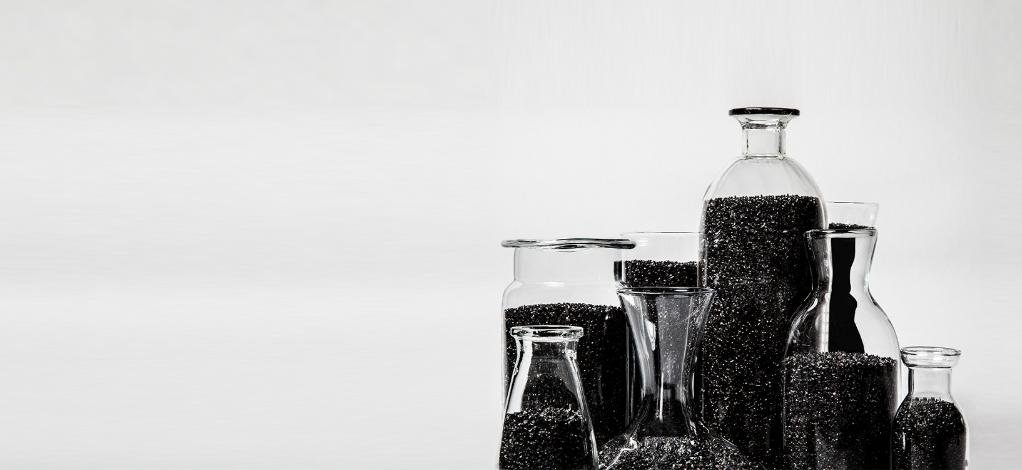
Conductive Carbon Black
Conductive carbon black is a very dry material with low flowability, widely used in lithium-ion batteries, as well as in sealing and insulation materials, rubber, electrodes, paints, and coatings. To ensure optimal performance, conductive carbon black must be completely free of metal impurities, as any metal particles in batteries can interfere with its conductivity. Magnetic separation can safeguard the quality of the raw materials without altering their core properties. Primarily, conductive carbon black is used to enhance the strength of tire rubber and serves as a pigment, UV stabilizer, and a conductive or insulating additive in various applications, including rubber, plastics, inks, and coatings.
Continuous Production Process
Carbon black production is a non-stop process that cannot tolerate any interruptions. To ensure smooth operation, manufacturers of products like lithium-ion batteries incorporate two self-cleaning magnets into their production lines.
The cleaning cycle takes just 18 seconds, during which the product is redirected through a bypass, ensuring continuous operation. At any given time, at least one magnet is active, and both magnets are in use 98% of the time.
These magnets effectively remove metal contaminants from battery-grade carbon black powder and are also suitable for materials with low flowability. The self-cleaning rotating magnets are capable of capturing iron particles larger than 21 µm. Their rotating design prevents the buildup of powder on the magnetic bars, ensuring better contact with the material and improving separation efficiency.
These magnets are ideal for installation in free-fall chutes, capable of withstanding temperatures up to 90°C. For applications requiring higher heat resistance, specialized magnet options are also available.
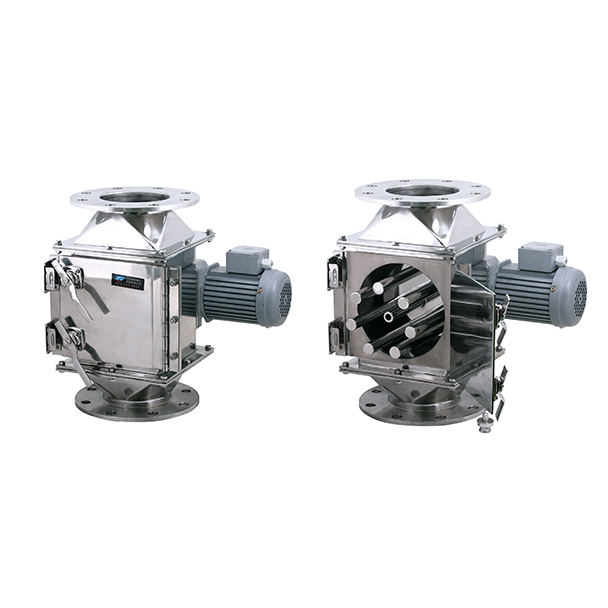